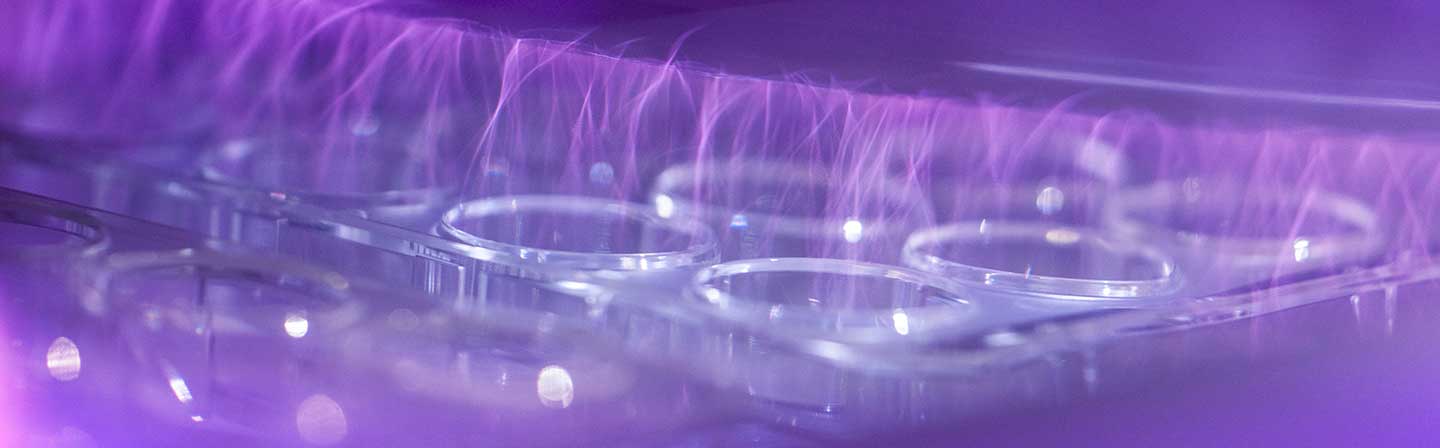
Project ”COOLBat”
In order to achieve future climate targets, CO₂ must be continuously reduced along the entire value chain and throughout the entire product life cycle. Innovative lightweight-construction materials and material combinations, manufacturing technologies and multifunctional structures can provide a significant contribution towards achieving these goals and, consequently, to the strengthening of Germany as a location for innovation.
The COOLBat project focuses on the development, optimization and scaling of lightweight-construction materials and technologies for battery systems, e. g. in electric vehicles. At the Fraunhofer IST, we are working on replacing environmentally harmful, expensive and barely recyclable thermally conductive pastes, which are utilized in the cooling of battery cells, with so-called thermally conductive mats. With the aid of a REACH-compliant procedure based on atmospheric-pressure plasma and electrochemical processes, thermally conductive mats are produced from natural-fiber foams with modified surfaces. Furthermore, the environmental impact of the battery housing and its components is being investigated at the Fraunhofer IST.
By means of a Life Cycle Assessment (LCA), all emissions over the entire life cycle of the housing are analyzed - from material extraction, through production and the use phase, and on to recycling. As a result, insights can be gained into which concepts could also be promising for industrial use in order to make the battery housing more environmentally friendly.
Through the reduction in the number of individual systems and the application of integral manufacturing processes, it is possible to reduce cost- and mass-intensive interfaces and energy-intensive joining technologies. With regard to the thermally conductive mats, the result is a flexible, thermally conductive lightweight-construction component for integration into the battery housing. Its manufacture is performed using cost-effective, resource-conserving and environmentally friendly materials and production processes. As a result, energy can be saved in the manufacturing and assembly process, and CO₂ emissions can be reduced during the use phase.