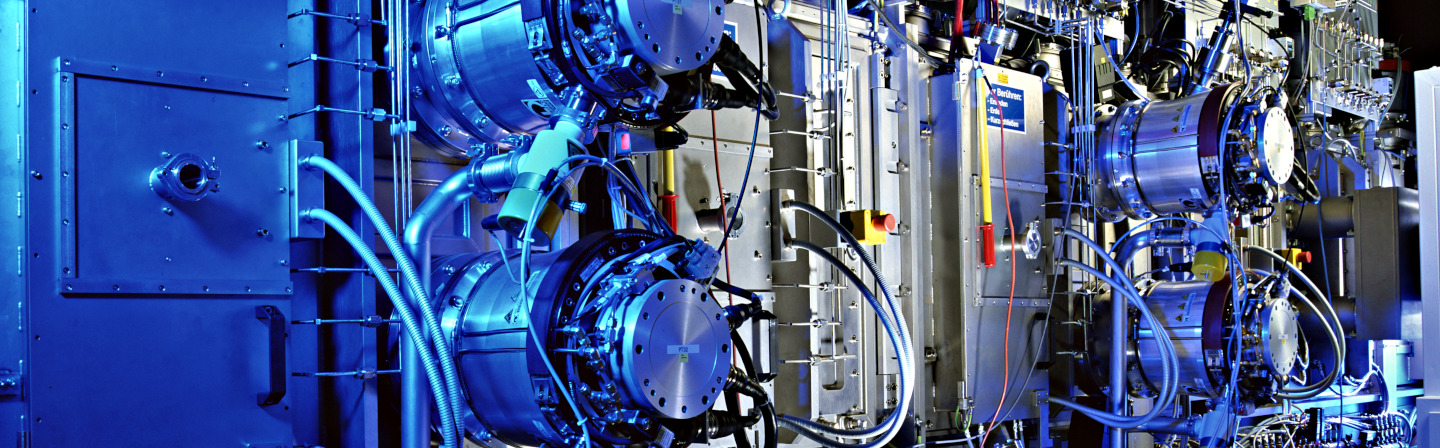
The Fraunhofer IST brings together unique expertise in the industrial use of magnetron sputtering. From applications for friction reduction or protection against corrosion and wear, through electrical and optical functions, and on to medical technology, the different variants of magnetron sputtering are utilized. Diverse coating sources, as well as process monitoring and active control, are applied and further developed at the Fraunhofer IST.
For development purposes, industrial coating facilities in batch and inline type with different source geometries (planar and cylindrical cathodes) for metallic and reactive deposition are available.
With the EOSS® (Enhanced Optical Sputtering System) sputtering systems, the Fraunhofer IST has ultra-modern equipment at its disposal for the production of precise optical interference filter systems. The layers are thereby applied to the substrate in up to three chambers by means of magnetron sputtering. As source materials, cylindrical tubes are utilized which, in contrast to their planar counterparts, exhibit a significantly more stable distribution function. For the further reduction of particle contamination, the entire system (see adjacent figure, lower section) was designed as a “sputter-up” concept. In such cases, coating takes place from the bottom upwards so that heavier particles cannot condense on the substrates. An additional station for plasma treatment and a powerful heating system round off the systems.
With the second generation of the system, coating can now also be carried out simultaneously from above. This allows a reduced process time for the production of optical filters with reverse-side coating. In addition, distortions caused by layer stress can be compensated for during filter deposition and even exceptionally thin substrates can be functionalized in this way.
The experts at the Fraunhofer IST utilize the A700V inline-sputter coating facility for the research and development of coatings and complex coating systems on an industrial scale. This ranges from material and process development of single layers through to systems of up to 10 different materials, e.g. for transparent conductive oxides (TCO), low-e layer systems, electrochromics, solar protection, fuel cells, interference optics on a large area or astronomy mirrors.
The Megatron® coating module developed at the Fraunhofer IST allows the rapid and variable realization of previously unattainable combinations of materials. Behind each of the two cylindrical tube targets, a further planar target is arranged. In the secondary sputtering process, atoms are detached from the planar target and “implanted” into the tube target. Titanium oxide, for example, can be doped with niobium and deposited. For certain material combinations, this results in an increased sputtering rate of up to 100 percent compared to the conventional process. The new module is ready for series production and can be retrofitted.