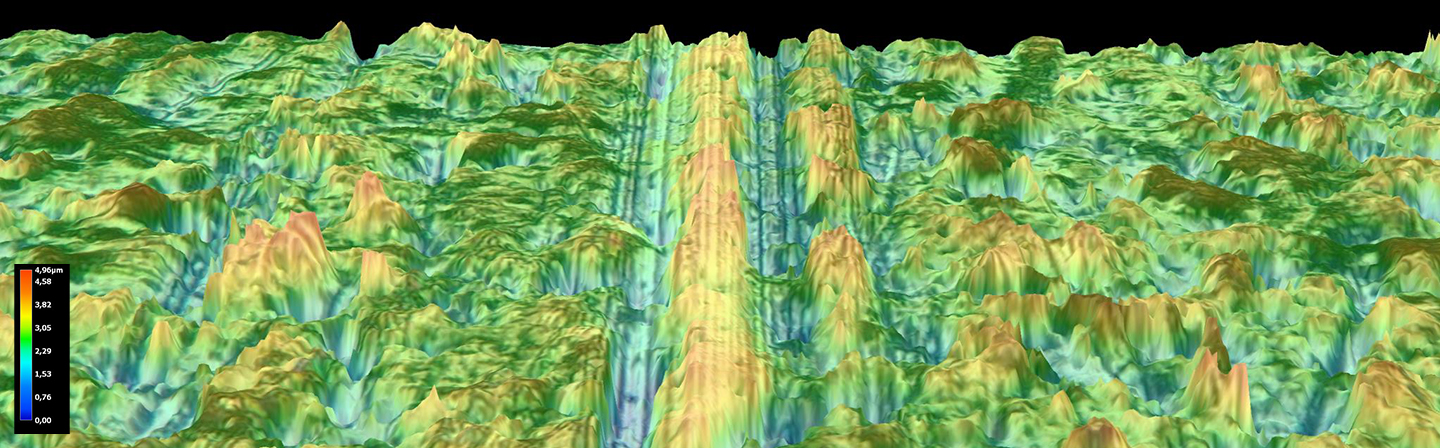
Mechanically stressed components are subject to a natural wear process. The consequences in terms of the extent and severity of this wear can be decisive for the efficiency and operation of a device such as a compressor in a heat pump. Our versatile preparation and analysis methods enable a comprehensive wear analysis. The causes and consequences of wear can thereby be precisely identified and evaluated. Through the meticulous examination of the wear phenomena, we are able to provide recommendations regarding the optimization of the performance capabilities and service life of the components.
Higher power consumption, lower compression and oil surge are undesirable consequences of wear in heat-pump compressors. The correct design, the utilization of the optimum material and, where appropriate, a suitable surface treatment can reduce the negative effects mentioned and extend the product service life. Our comprehensive wear analysis allows you to efficiently optimize your products. Together, we identify effective improvement measures. You and your customers benefit from your quality product.
Our experts would be delighted to answer your questions and to find individual solutions for your specific requirements.