A look behind the scenes - The “COOLBat” project
To improve the efficiency of battery storage systems whilst simultaneously minimizing the environmental impact - that was the goal of the joint project “COOLBat”, on which a total of 15 research institutions and industrial partners worked in collaboration. Innovative materials and processes were applied with the aim of improving the service life and performance of batteries. Today, we are talking to Hannes Lefherz, an employee at the Fraunhofer IST, about the project and the role of the Fraunhofer IST within the consortium.
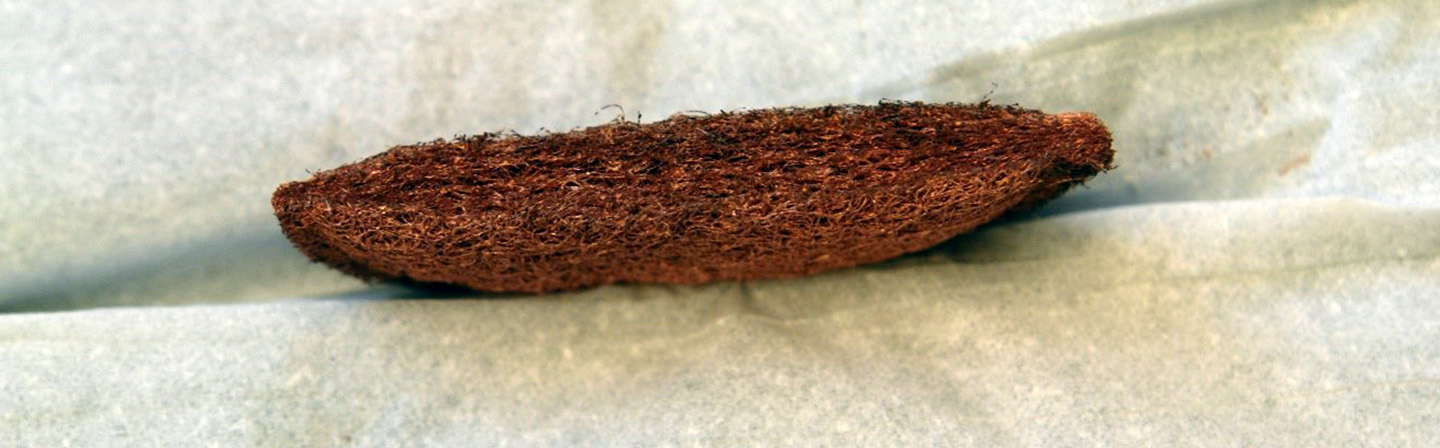
Hannes, what exactly was the COOLBat project about, what prompted its initiation and who is involved?
The goal of the “COOLBat” project was, in collaboration with our project partners, to develop an innovative battery housing that can be repaired and dismantled more easily. In addition, it should be lighter than a comparable housing, easier to reuse and, as a result, more environmentally-friendly overall. To achieve this, an interdisciplinary team led by the Fraunhofer Institute for Machine Tools and Forming Technology IWU developed individual components and assembled them to form a functioning battery housing. Further partners of the Fraunhofer IST in the “COOLBat” project were Auto-Entwicklungsring Sachsen FES/AES, INVENT GmbH, Compositence, iPoint-systems GmbH, TIGRES GmbH, LXP Group GmbH, Basdorf, Lampe & Partner GmbH, MID Solutions GmbH, Synthopol Chemie Dr. rer. pol. Koch. GmbH & Co. KG, TRIMET Aluminum SE and Mercedes-Benz AG as well as the Fraunhofer Institute for Manufacturing Technology and Advanced Materials IFAM and the Fraunhofer Institute for Wood Research, Wilhelm-Klauditz-Institut WKI.
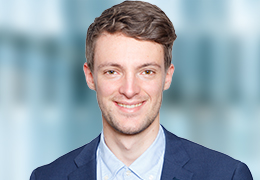
What was the specific contribution made by the Fraunhofer IST to the project?
The Fraunhofer IST was responsible for two tasks within the project: the development of a metallized thermally conductive mat and the comprehensive environmental assessment of the entire system.
During the development of the thermally conductive mats, the institute focused on renewable raw materials. Various substrates were considered and the final decision was made in favor of a mat based on coconut fibers. The surface of the fibers was plasma treated and metallized, as a result of which their thermal conductivity was greatly improved.. Another advantage of using a thermally conductive mat over thermally conductive pastes is the ease with which the mat can be disassembled, which not only allows the mat to be re-used, but also makes it much easier to disassemble the entire battery system.
In order to ensure that the newly developed battery housing concept is generally more environmentally friendly, a life cycle assessment model was developed in collaboration with partner “iPoint“ as part of an environmental evaluation of the overall system. Using a variety of parameters and scenarios, the environmental impact of the individual components and the system as a whole could be investigated. The results of the assessment are made available to the project partners via an interactive online tool. With this tool, they can identify the most important influencing parameters and thus more easily integrate the sustainability perspective into the development of components.
What results have you achieved?
It has been shown that the developed battery housing can lead to a significant reduction in greenhouse gas emissions once it is integrated into a circular economy. The reuse of components such as the inner support structure, the base module and the carbon fiber cover, as well as the remanufacturing of the battery housing, have a particularly high potential for reducing the environmental impact.
What role did you play in the project and what did you personally enjoy about your work within the team?
My task was to develop the model for the ecological life cycle assessment and to coordinate the cooperation with our partner iPoint. What I really like about these kinds of cross-cutting projects is that you get an exciting insight into the manufacturing processes of innovative technologies. In the “COOLBat“ project, for example, it was fascinating to see that aluminum can be foamed and that coconut fibers can be coated in such a way that they are interesting for utilization in electronic components.
What happens now? Are follow-up projects planned?
Unfortunately, funding for research projects in the field of battery research has been greatly reduced, so no concrete follow-up projects are currently planned. I would like to see Germany once again investing more in research into the battery, which is an important technology for the future, so that the battery housing can be further developed.
Last modified: