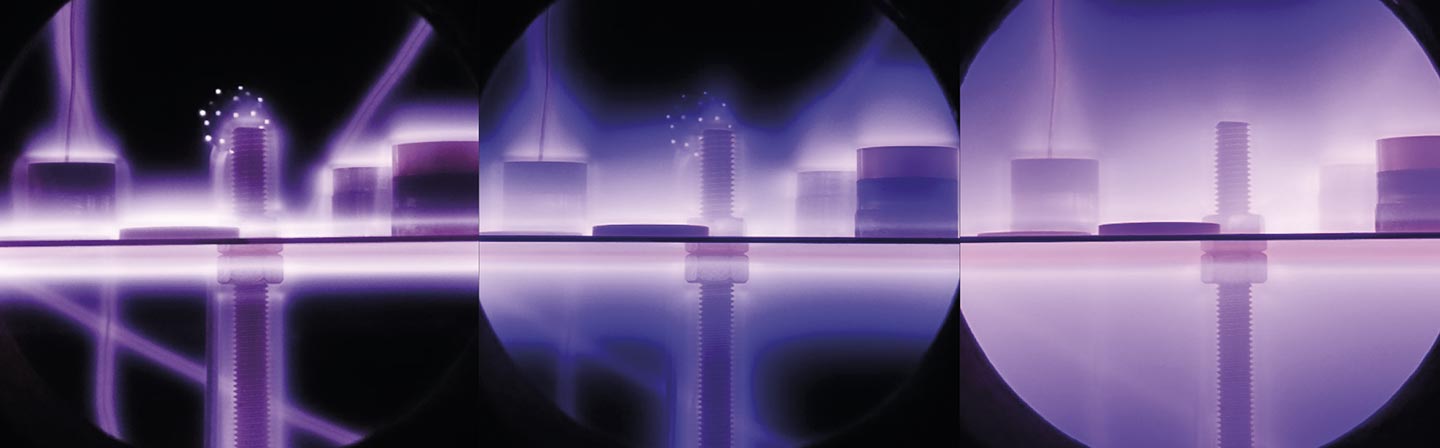
Bei der Produktion von Zerspanungswerkzeugen entstehen Oberflächen- und Randschichtzustände, die für eine nachfolgende Beschichtung eine möglichst effiziente Reinigungsprozedur erfordern. Um neben der Vermeidung entsprechend aggressiver nasschemischer Reiniger auch weitere technologische Vorteile zu generieren, war das Fraunhofer IST in einem DBU-Verbundprojekt gemeinsam mit Partnern aus Industrie und Forschung erfolgreich an der Erarbeitung und Evaluierung einer alternativen Reinigungsprozesskette beteiligt.
Die entwickelten Kombinationen aus aufeinander abgestimmten Vorbehandlungsprozessen ermöglichen eine hohe Reinigungswirkung bei deutlich reduzierter Umweltbelastung. Gleichzeitig sind zusätzliche technologische Funktionen wie die Einstellung der Schneidkantengeometrie bei geometrisch komplexen Zerspanungswerkzeugen möglich. Dies ergibt eine wirtschaftliche Alternative zu herkömmlichen Reinigungsprozessen.
Um die Prozesssicherheit der in der Produktion nachfolgenden Vakuumbeschichtungsprozesse zu steigern, wurden folgende Einzelverfahren in unterschiedlicher Verkettung untersucht und mithilfe von Zerspanungsversuchen evaluiert:
Als Weiterentwicklung des State of the Art in der Produktion wurde für das wässrige Reinigungsverfahren ein zweistufiges Reinigungskonzept so gewählt, dass der größtmögliche Effekt mit der kleinstmöglichen Einsatzmenge erreicht wird. Die intelligente Wirkstoffkombination hält die pH-Werte der eingesetzten wässrigen Reiniger in einem moderaten neutralen Bereich und lässt sich biologisch abbauen. Das Arbeiten mit dem auf Überschallgeschwindigkeit beschleunigten CO2-Schneestrahl ermöglicht die effiziente und schonende Entfernung partikulärer und filmischer Verunreinigungen wie u. a. Staub, Rückstände von Polierpasten, Öle oder Schneidemulsionen. Dieses Verfahren kann automatisiert und lokalisiert für die Reinigung schwer zu erreichender Geometriebereiche eingesetzt werden.
Beim Plasmaelektrolytischen Polieren (PEP) wird das zu behandelnde Bauteil in einem Elektrolyt aus nichttoxischen Salzen und Wasser durch Anlegen einer Spannung von einigen 100 V gereinigt und poliert. Neben sehr guten Reinigungsergebnissen werden Grate und Verunreinigungen im gleichen Prozessschritt entfernt. Außerdem lassen sich die Schneidkantenradien der Werkzeuge gezielt einstellen.
Für den letzten Schritt der Vorbehandlung wird die Substratoberfläche unter Vakuumbedingungen mittels plasmachemischer und plasmaphysikalischer Prozesse von jeglichen chemischen Verbindungen von der Mikro- bis zur Nanometer-Skala befreit und chemisch aktiviert. Vor allem für die Anbindung bzw. Haftung nachfolgend aufgetragener Schichten spielt dies eine wesentliche Rolle. Ausschlaggebend für eine effektive Reinigung sind dabei die vorherrschenden Plasmabedingungen, die in weiten Bereichen durch Variation der Pulsgeometrie, Beschleunigungsspannungen und Plasmaleistung modifiziert werden können (vgl. Abbildung oben).
In der Entwicklung der Verfahrenskette wurden verschiedene Einzelverfahrenskombinationen an künstlich verschmutzten Zerspanwerkzeugen appliziert. Um eine bestmögliche Vergleichbarkeit herzustellen, wurde dazu eine synthetische Referenzverschmutzung aus Ölen, Fetten, Partikeln und Suspensionen der relevanten Fertigungskette entwickelt. Vor der Evaluierung wurden die Werkzeuge bezüglich Schneidkantenradien und Oberflächenrauheit sowie die Schichthaftung qualifiziert. Die maximale Standzeit der Werkzeuge wurde dann in einer Zerspanungsuntersuchung bestimmt.
Eine Bewertung der Ergebnisse zeigt den direkten Einfluss der Einzelverfahren in der jeweiligen Kette:
Dieser Beitrag ist Teil des Jahresberichts 2019.