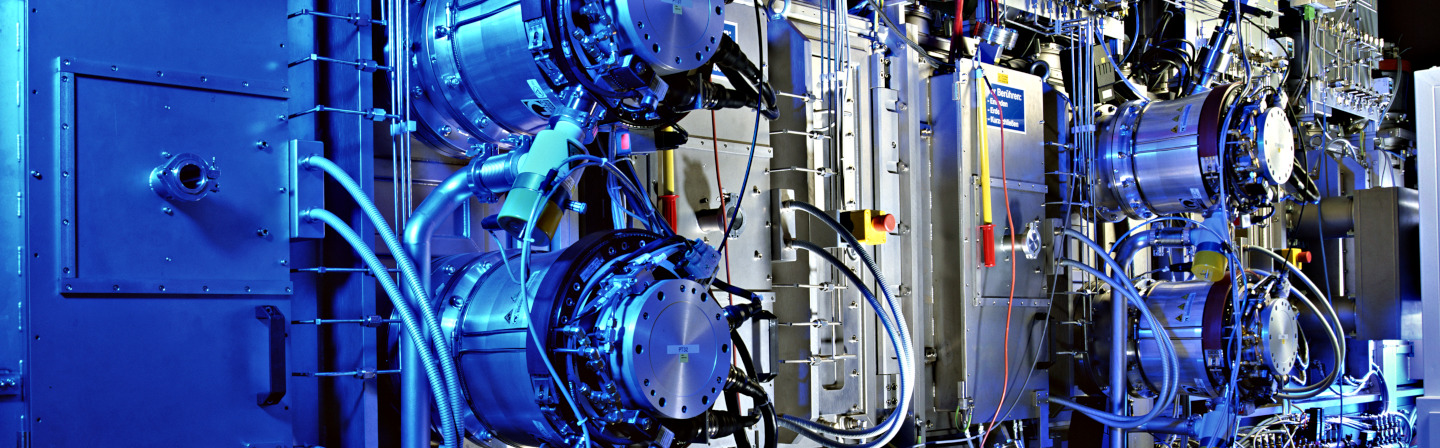
Das Fraunhofer IST bündelt eine einzigartige Expertise im Bereich der industriellen Nutzung des Magnetronsputterns. Von Anwendungen zur Reibungsminderung, Korrosions- und Verschleißschutz über elektrische und optische Funktion bis zur Medizintechnik werden die unterschiedlichen Varianten des Magnetronsputterns eingesetzt. Verschiedene Beschichtungsquellen sowie Prozessüberwachung und aktive Regelung werden am Fraunhofer IST eingesetzt und weiterentwickelt.
Für die Entwicklung stehen industrielle Beschichtungsanlagen in Batch- und Inline-Typ mit verschiedenen Quellengeometrien (planar und zylindrische Kathoden) für die metallische und reaktive Abscheidung zur Verfügung.
Mit den Sputtersystemen des Typs EOSS® (Enhanced Optical Sputtering System) stehen dem Fraunhofer IST hochmoderne Anlagen zur Verfügung, um präzise optische Interferenzfiltersysteme herzustellen. Dabei werden die Schichten in bis zu drei Kammern durch Magnetron-Sputtern auf das Substrat aufgebracht. Als Quellmaterialien werden zylindrische Rohre eingesetzt, welche im Gegensatz zu ihren planaren Pendants eine deutlich stabilere Verteilungsfunktion aufweisen. Zur weiteren Verminderung von Partikelkontaminationen wurde die gesamte Anlage (siehe nebenstehende Abbildung unten) als »Sputterup«-Konzept ausgelegt. Die Beschichtung erfolgt in diesem Fall von unten nach oben, so dass schwerere Partikel nicht auf den Substraten kondensieren können. Eine zusätzliche Station zur Plasmabehandlung und ein leistungsstarkes Heizsystem runden die Systeme ab.
Mit der zweiten Generation des Systems (siehe nebenstehende Abbildung oben) können nun auch gleichzeitig Beschichtungen von oben durchgeführt werden. Das erlaubt eine reduzierte Prozesszeit bei Produktion von optischen Filtern mit Rückseitenbeschichtung. Außerdem können Verbiegungen durch Schichtspannung schon während Filterabscheidung kompensiert werden und auf diese Weise auch besonders dünne Substrate funktionalisiert werden.
Die Experten am Fraunhofer IST setzen die Inline-Sputter-Beschichtungsanlage A700V zur Forschung und Entwicklung von Schichten und komplexen Schichtsystemen im industriellen Maßstab ein. Dies reicht von der Material- und Prozessentwicklung von Einzelschichten bis hin zu Systemen aus bis zu 10 unterschiedlichen Materialien, z. B. für transparent leitfähige Oxide (TCO), Low-e-Schichtsysteme, Elektrochromie, Sonnenschutz, Brennstoffzellen, Interferenzoptiken auf großer Fläche oder Astronomiespiegel.
Das am Fraunhofer IST entwickelte Beschichtungsmodul Megatron® erlaubt die schnelle und variable Realisierung von bisher nicht herstellbaren Materialmischungen. Hinter jedem der zwei zylindrischen Rohrtargets ist ein weiteres planares Target angeordnet. Im sekundären Sputter-Prozess werden Atome vom planaren Target gelöst und in das Rohrtarget »implantiert«. So lässt sich z. B. Titanoxid mit Niob dotieren und abscheiden. Für bestimmte Materialkombinationen ergibt sich eine erhöhte Sputterrate von bis zu 100 Prozent gegenüber dem herkömmlichen Prozess. Das neue Modul ist serienreif und nachrüstbar.